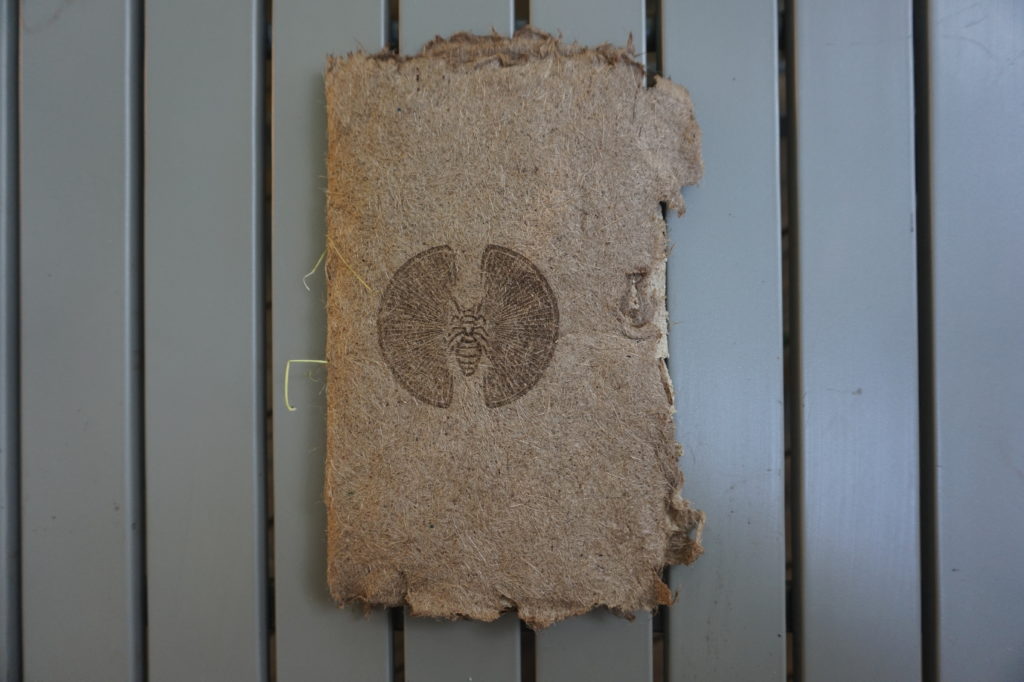
Zines have been around for a longtime with the goal being to make something cheap and easy to reproduce. This means there’s a big reliance on printer paper and classic photocopier inks. Though this can make production easy it also means that it’s not the most environmentally friendly situation. Bleached printer paper takes a long time to break down, inks and toners are can be fairly toxic and create environmental issues.
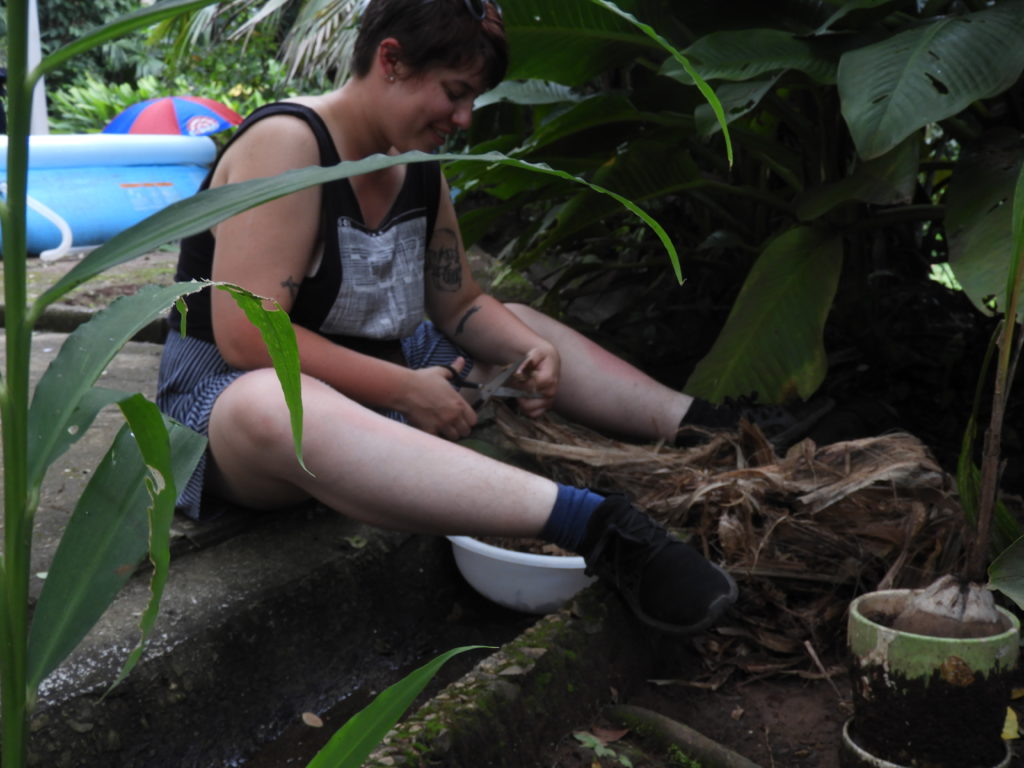
During DinaCon my goal was create a fully sustainable zine. My concept of sustainability was making something that would have little environmental impact and have the ability to break down easily as time goes by. This meant that I committed to foraging for materials to make paper, inks and binding for a zine.
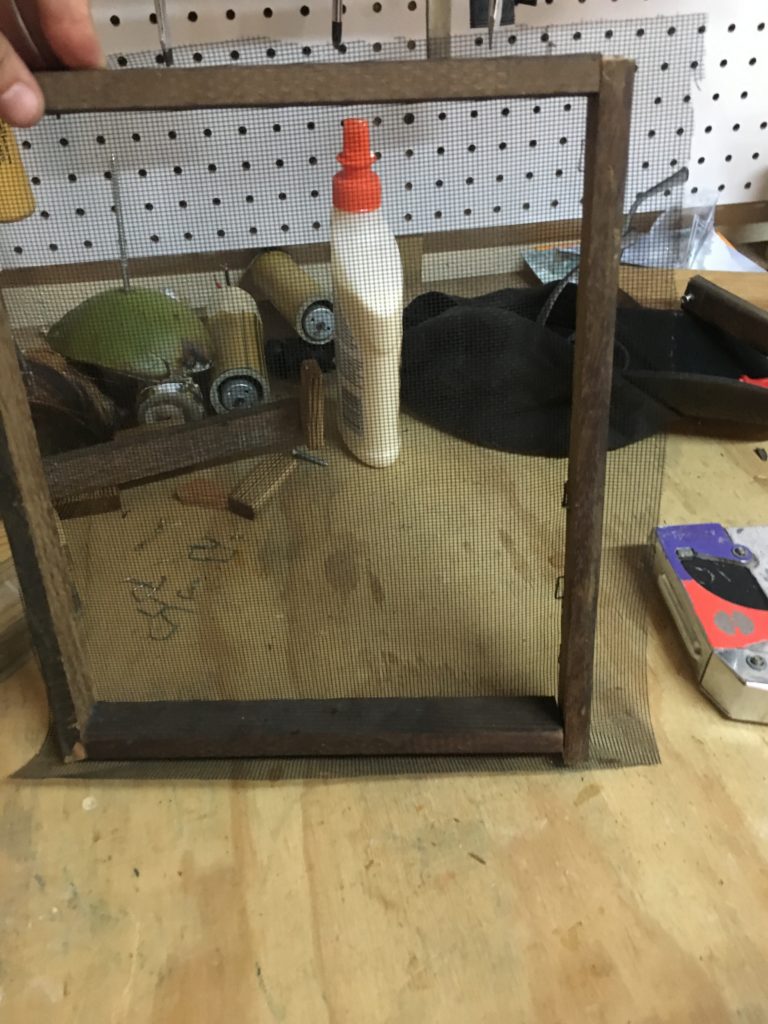
Here’s a breakdown the components and the processes involved with each part:
Mould – I made my paper mould on-site using scrap wood provided by Andrew Coates’ building team and screen that was DinaLab. This took two days.
Brown Paper – Foraged banana tree bark, boiled for two hours and then blended to get pulpy. This was then put in a large plastic packing container with a 2:1 water to pulp ratio called a slurry. It took about 4 days of pulling and drying to make 12 sheets of paper.
White Paper – Foraged turkey tail mushrooms from a local trail thanks to Blackii’s suggestion, blended with water to get pulpy. This was then put in the large plastic container with the 2:1 water to pulp ratio slurry. It took 5 days of pulling and drying with a dehumidifier’s help due to the natural moistness of mushrooms to get 7 sheets of paper.
Black Ink – Foraged charcoal from a small fire, ground down and mixed with gum arabic to thicken. Gum arabic was the one item I brought with me from home, I wasn’t sure how much access I would have to a similar product. This took about 15 minutes
Blue/Green Ink – Algae pigment provided by the wonderful Elliot mixed with water/agar agar and gum arabic to try different textures and thicknesses. Each ink option took a few minutes to mix.
Brown Ink – This was made by boiling down rumbutan skins for one hour to get a gorgeous deep red burgundy and then mixing it with agar agar. This took one hour and 10 minutes to make.
Clear Ink – Mix of honey and coffee which made a transparent reflective ink which took the same amount of time as making a pot of coffee.
Wing Page – All the wings on the centrefold pages were foraged from different dead insects other dinasaurs used for their own experiments and projects. Once they were no longer being used I removed the wings and put them in the slurry and pulled the sheet with the wings embedded.
Bindings – The bindings are foraged vines from a plant in the backyard of DinaLab that I sewed through the pages for an easy bind. This took about ten minutes.
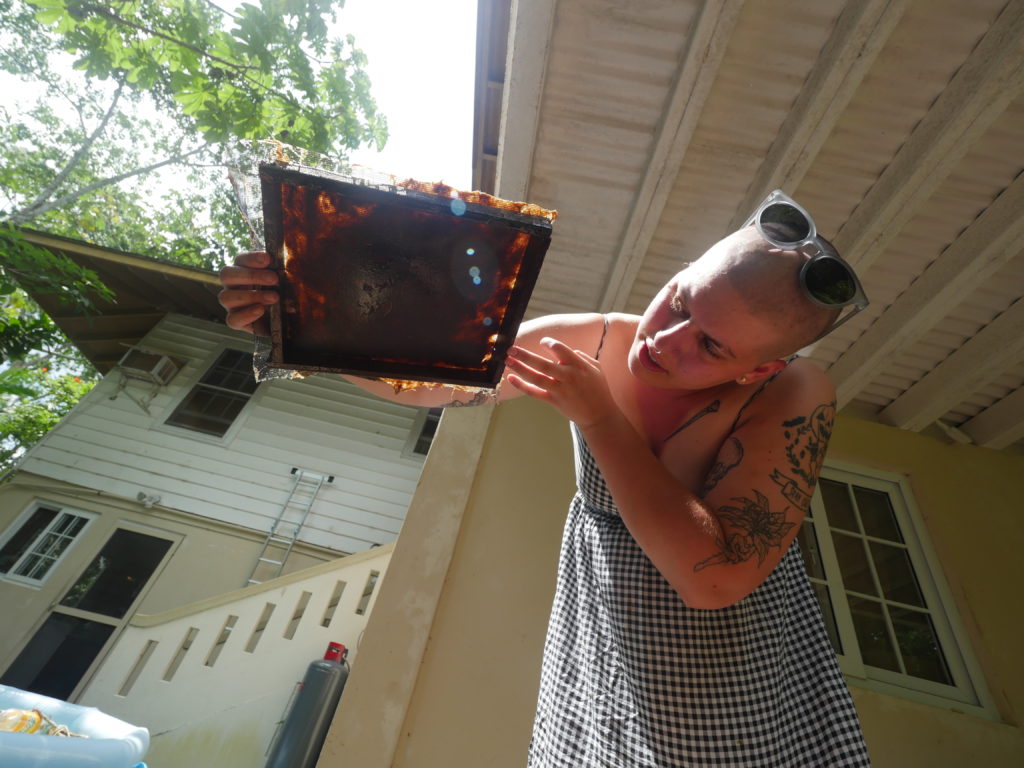
The final zine was quite successful. It will be left to slowly degraded on its own to see how well the handmade zine lasts and breaks down. The content is entirely inspired by DinaCon, it’s attendees, the connections I made, experiences I had and has become a love letter to my time in Gamboa this summer. A special thank you to Andy Quitmeyer, Rob Faludi, Blackii Migliozzi, Elliot Roth, Ramy Kim, Ananda Gabo, Joetta Gobell, Lee Wilkins, Ashlin Aronin, Amanda Savage, Stephanie Rothenberg, Seamus Kildall, Andrew Coates and every other dinasaur that I had the absolute pleasure of sharing space with for all the inspiration and help.